That is why automotive suppliers are equipping their products, such as bumpers, spoilers and other exterior components, with more and more functions. Meeting the increasing demands on safety for all traffic participants requires complex and safe test systems. In addition to test systems for interior fittings, Berghof Automation has also developed automotive exterior testing as its core competence. The company’s portfolio includes, among other things, test systems for testing bumpers and spoilers.
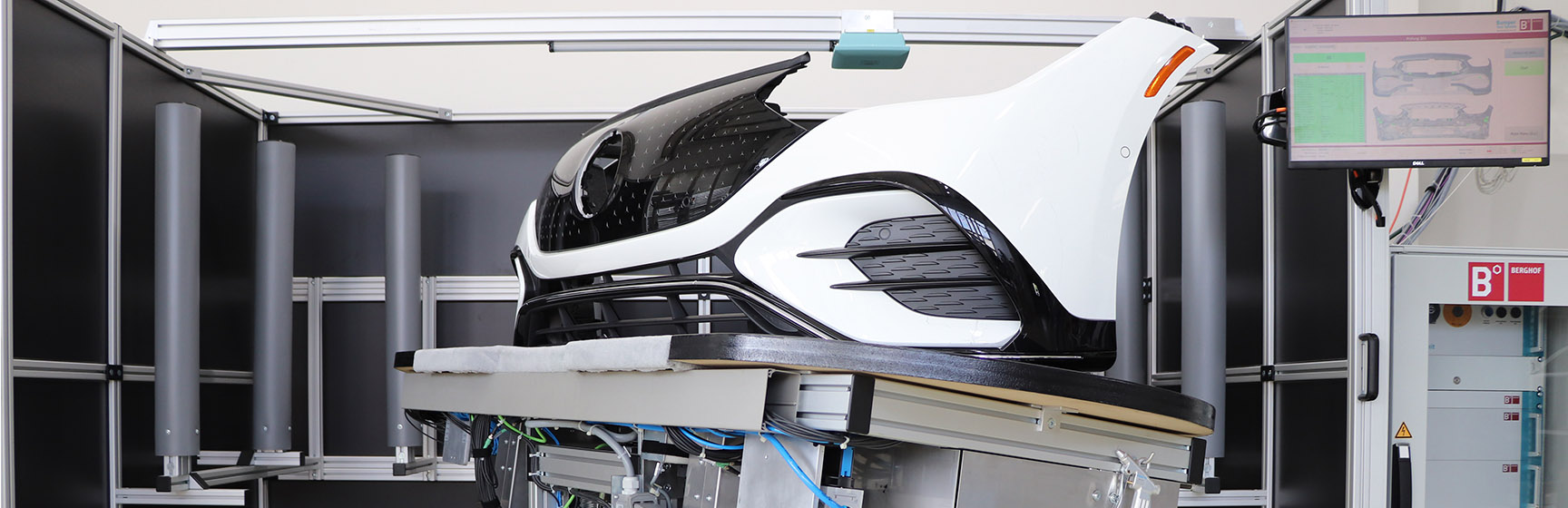
Automotive Exterior - Intelligent concepts, intelligently tested
With regard to technologies such as automated driving, and also future autonomous driving, car manufacturers are facing the task of developing intelligent safety and comfort systems more than ever – not only to protect car passengers but also to protect other traffic participants, such as pedestrians and cyclists.
Bumpers
Sensors in the bumper are an important contribution to additional safety in road traffic. These days they often contain highly complex safety-related features, such as distance and lane departure assist, sensors for detecting pedestrians and cyclists or blind spot assist. So that this sophisticated technology works smoothly in the end customers’ bumper, Berghof Automation has developed the bumper tester for automotive suppliers. Thus, we are making our contribution to making road traffic safer and more comfortable.
You have the choice between three expansion levels: the simple test table, the highly standardized, extremely variable test system for electrical bumper testing and the fully automated robot test system with a cycle time of less than 45 seconds.
All variants of bumper testing at a glance
In our new brochure “Bumper Testing Product Information” (PDF) in the download area “Test and inspection technology” you will find all the details about our three different bumper test systems.
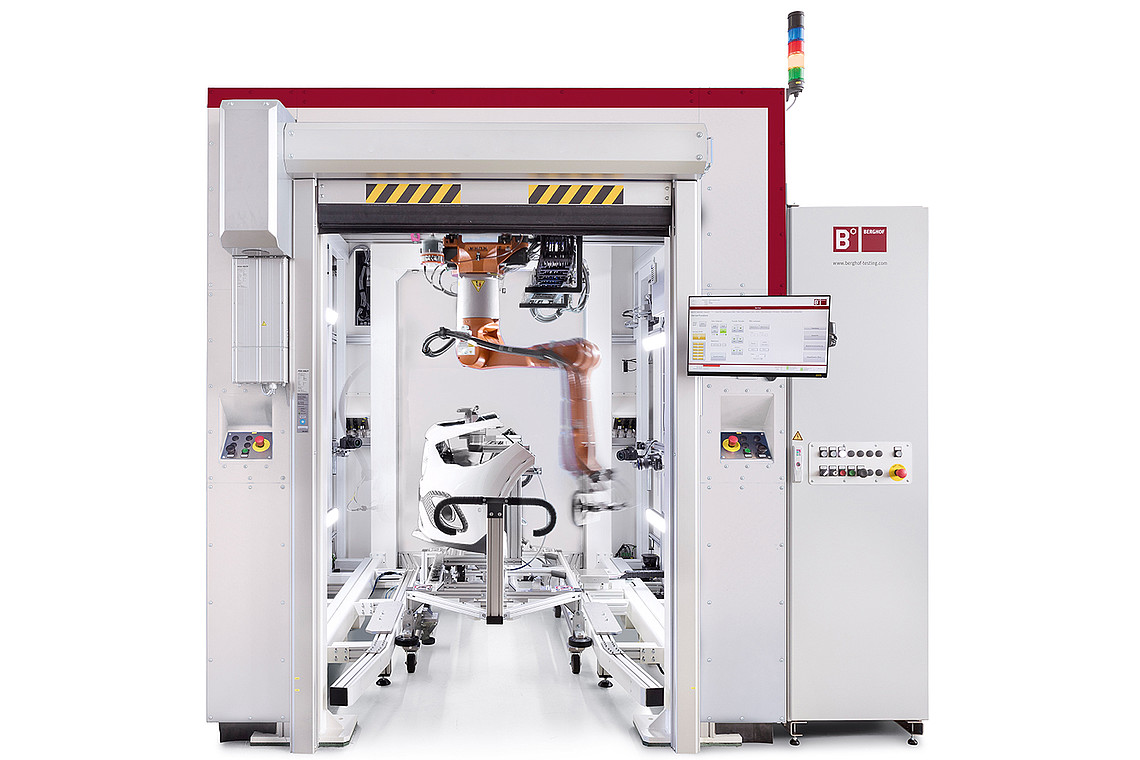
Bumper tester ALL-IN-ONE: Bumper test system with integrated mounting device
With our new bumper testing system, we combine the elementary assembly steps (trims, covers, OEM symbol, etc.) with the possibility of testing all electrical components in parallel.
The big advantage: instead of two stations, you only need one. This not only saves time and space, but of course also costs.
The mounting fixture can also be flexibly adjusted and tilted during the work. This makes it child's play to mount components on the outside and inside.
In compliance with current test specifications, the ALL-IN-ONE bumper tester features automatically adjustable impact obstacles for functional testing of the ultrasonic sensors. Nevertheless, the cycle time for a complete test remains under 30 seconds, even with lowering and retracting the impact obstacles.
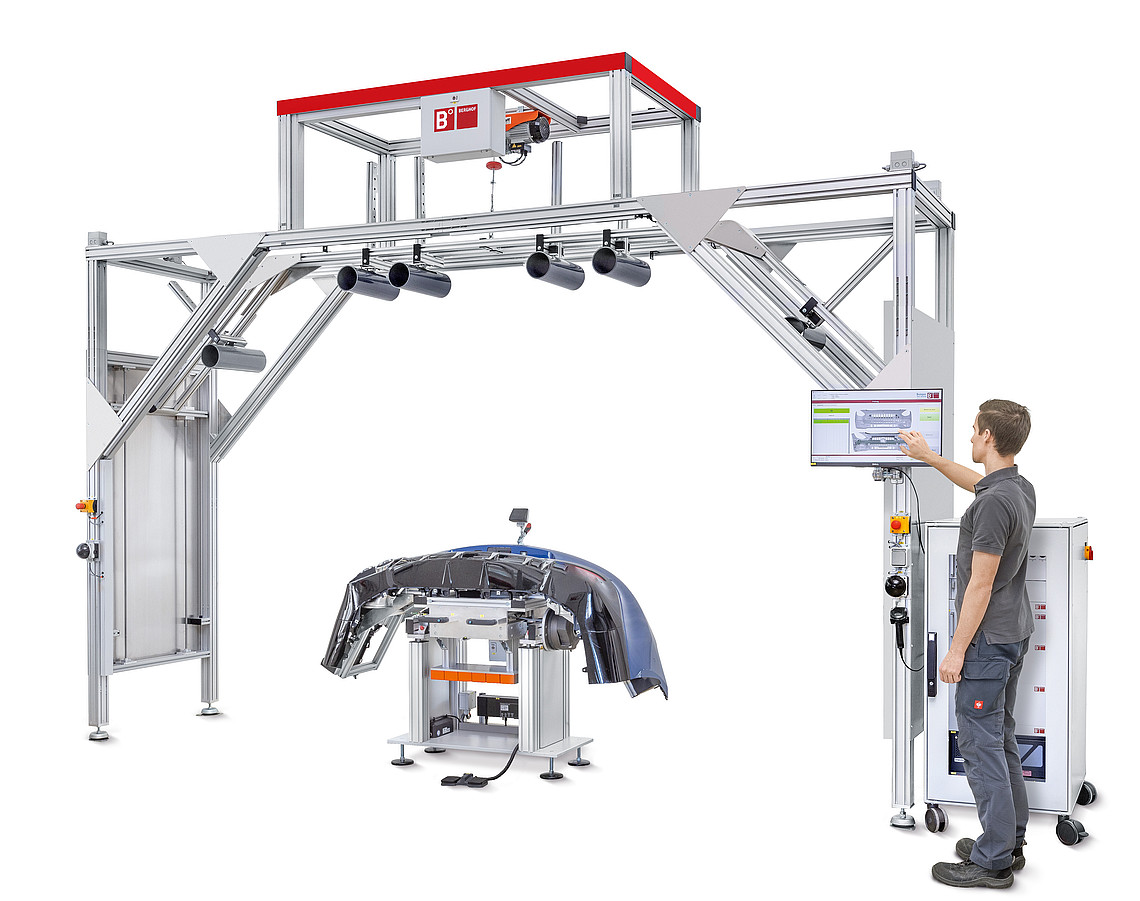
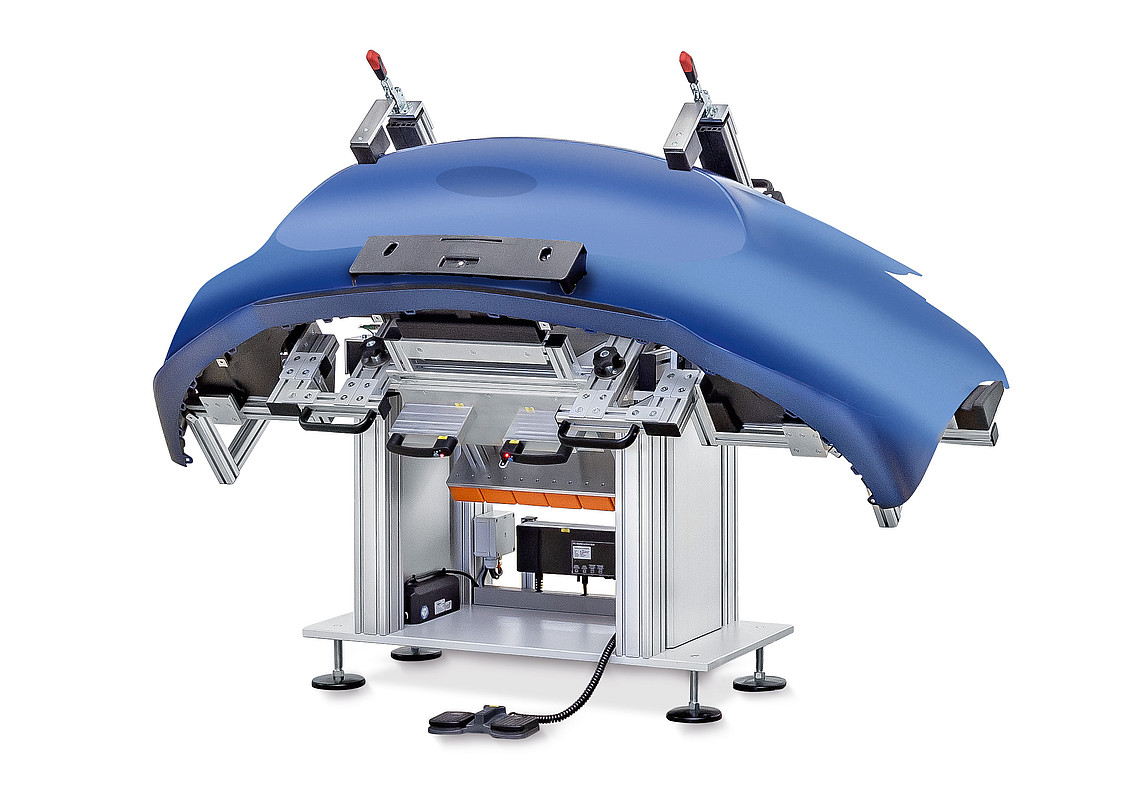
Based on proven technology
Based on LIN and CAN communication, the ALL-IN-ONE bumper tester precisely performs all required resistance, current and voltage measurements on the bumper.
The system electrically checks the proper functioning of both the lighting and safety components as well as all radar and ultrasonic sensors of the bumper.
The heart of the test system is our in-house Berghof test and inspection software. It tests bumpers reliably, documents the results of the test runs, prepares them graphically in a simple and clear manner, and stores them in a database system.
Thanks to the graphical user interface, the system is also intuitive and easy to operate.
Your advantages at a glance:
- Time savings of up to 30 seconds per test item due to fusion of test and assembly equipment
- Significantly lower space and investment requirements
- Flexible adjustable assembly table
- Integrated function test with variably adjustable impact obstacles
- Integrated test system (measurement technology, mechanics)
- Simple operation of the test interface
- Graphical display of the IO/NIO results
- Results storage in a database system
- Variant-related test parameter sets
- Predictive Maintenance
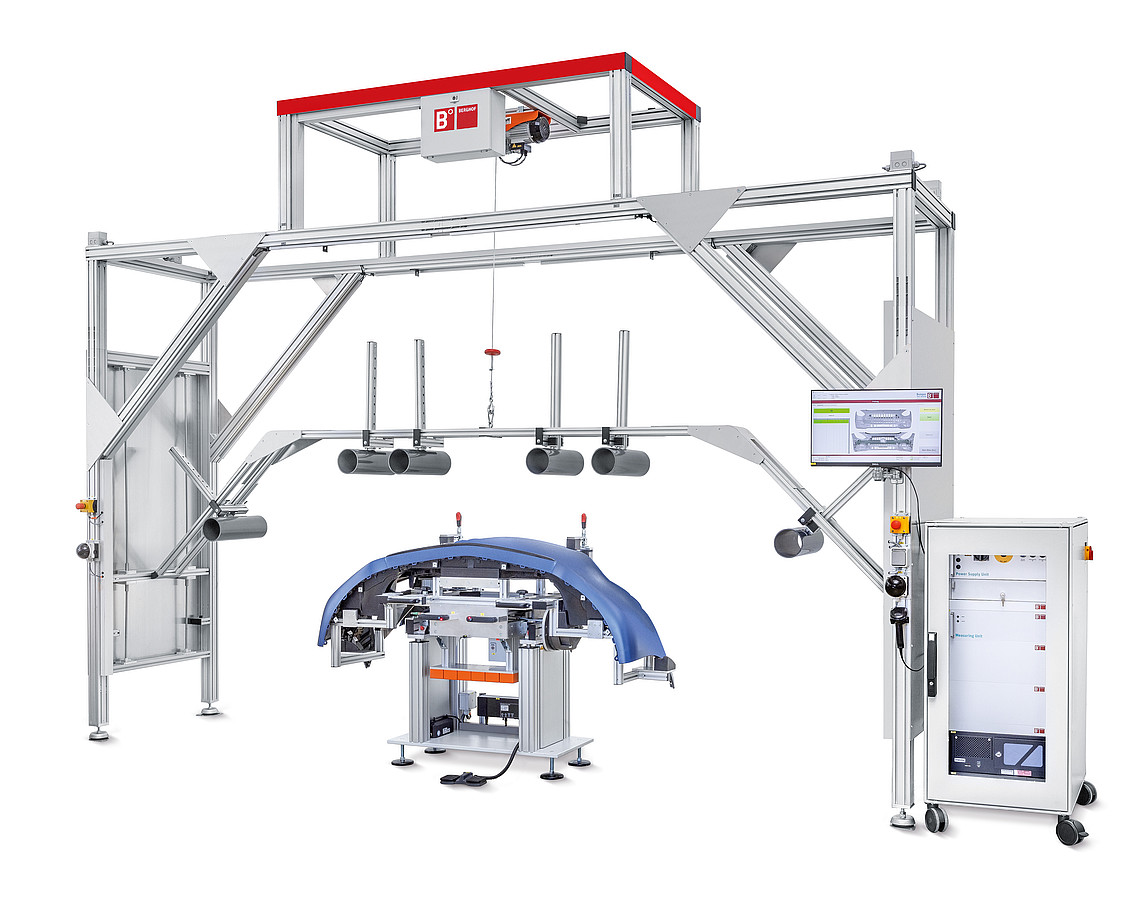
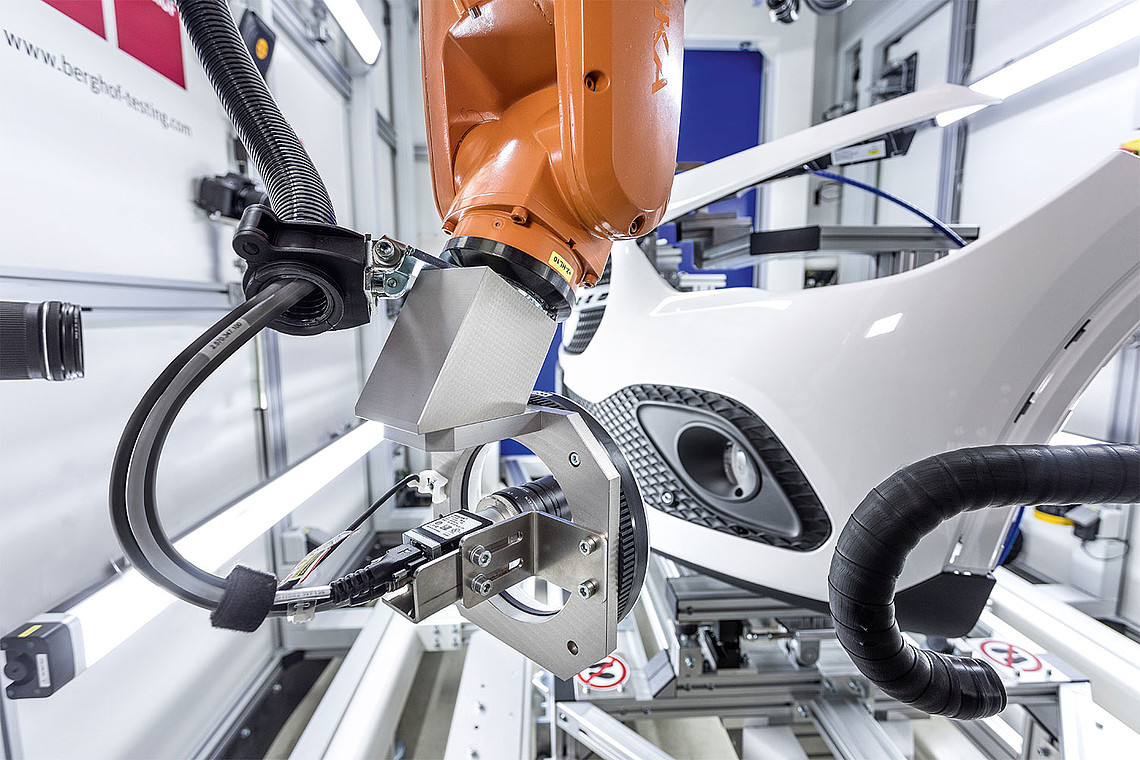
Application report "Bumper Tester ROBOTIC": Electrical and optical bumper testing – fully automated, fast, highly flexible
In recent years Berghof Automation has made a name for itself with its testing competence in quality management of bumper manufacturers. Now the bumper test system achieves new benchmarks in terms of cycle time, flexibility and degree of automation. The biggest highlights: With the help of a driverless transport system, the test stand can be operated completely workerless. And: Thanks to a tracking shot completely without intermediate stops, the testing robot can handle a full 55 inspection features in a cycle time of less than 45 seconds.
Would you like to learn more about our latest test system for fully automated bumper testing? Then read more about it here!
"Bumper Tester ELECTRIC": Electrical bumper test – highly standardized, minimum operating effort
Berghof Automation complements its test system portfolio with another test system for intelligent bumper testing. The highlights: The system is highly flexible, tests regardless of variant – in a cycle time of less than 30 seconds. The test system for electrical bumper testing has a standardized coupling, which makes it possible to mount every conceivable test item variant into the test system – current and future, front and rear bumpers – at the same time on a single system.
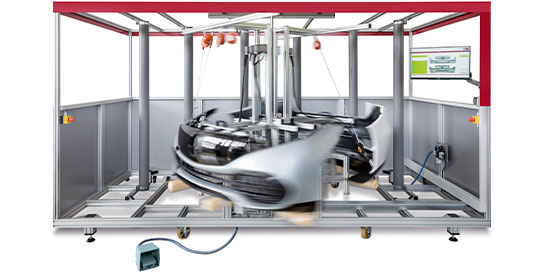
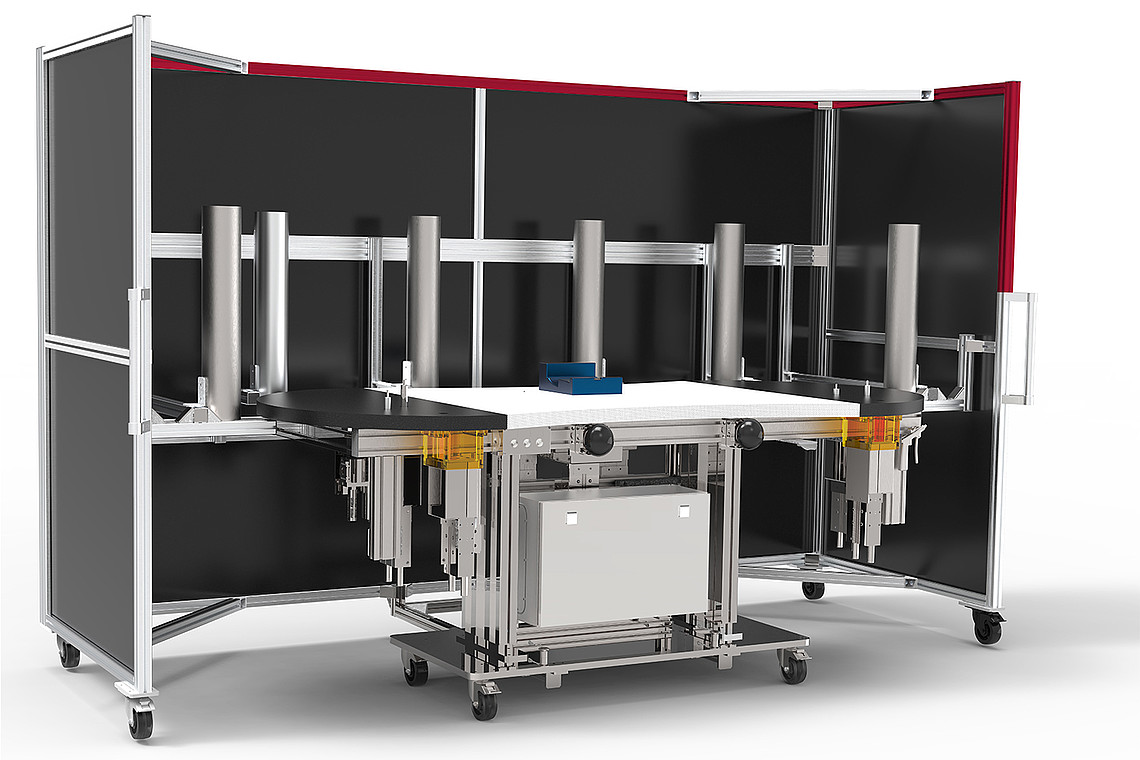
"Bumper Tester BASIC": The basic system for bumper testing
- Identification, completeness and surface of the bumper
- Electrical testing (functional check) of all radar and ultrasonic sensors
- Visual inspection of the correct mounting position of the pedestrian protection hose
- Visual presence and version check of the mechanical components (attachments, clips, chrome parts)
- Visual documentation after the testing
- Testing the lighting and safety components
- Resistance, current and voltage measurement, LIN and CAN communication, visual inspection
- Automatic or manual operation
Your advantages
- High variability: complete test system (measurement technology, mechanical components and testing robots with image processing) or integration into an existing assembly line
- Speed: optimized test sequence for a short cycle time
- Simple operation of the testing interface, graphic representation of the OK/NOK results
- Storage of results in a database system
- Version-based testing parameter sets
- Service features for quickly rectifying production faults
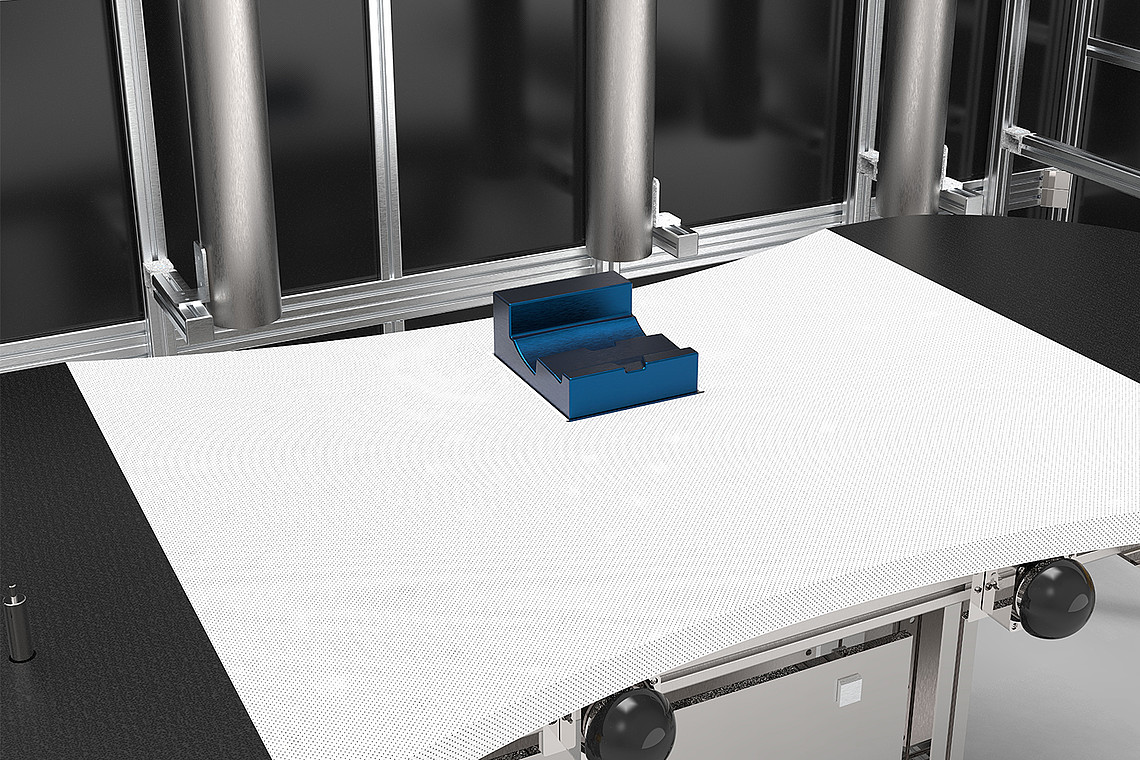
Downloads for our bumper portfolio
- To the brochure "Bumper testing product information" (PDF) in the Test and inspection technology download area
- To the case study "EOL Bumper Tester" (PDF) in the Test and inspection technology download area
- To the case study "Electrical Bumper Test" (PDF) in the Test and inspection technology download area
Spoilers
Spoilers on vehicles by no means exist only for visual reasons: They ensure that the air flows over the vehicle in a way that improves its aerodynamics. They do this by reducing the vehicle’s lifting force, thereby improving the driving properties – such as the driving stability, the cornering speed and the braking distance.
This makes the spoiler as well as the bumper a safety-related component of a vehicle. This makes it all the more important that all spoiler components are correctly positioned to ensure the optimal function. That is why Berghof Automation offers a test system for testing spoilers in all relevant parameters after production.
Thereby, we can make full use of our power of innovation and our testing expertise: In cooperation with a renowned automotive supplier for spoilers, we have developed a completely new type of testing concept that saves the customer about half of the space required and therefore also costs.
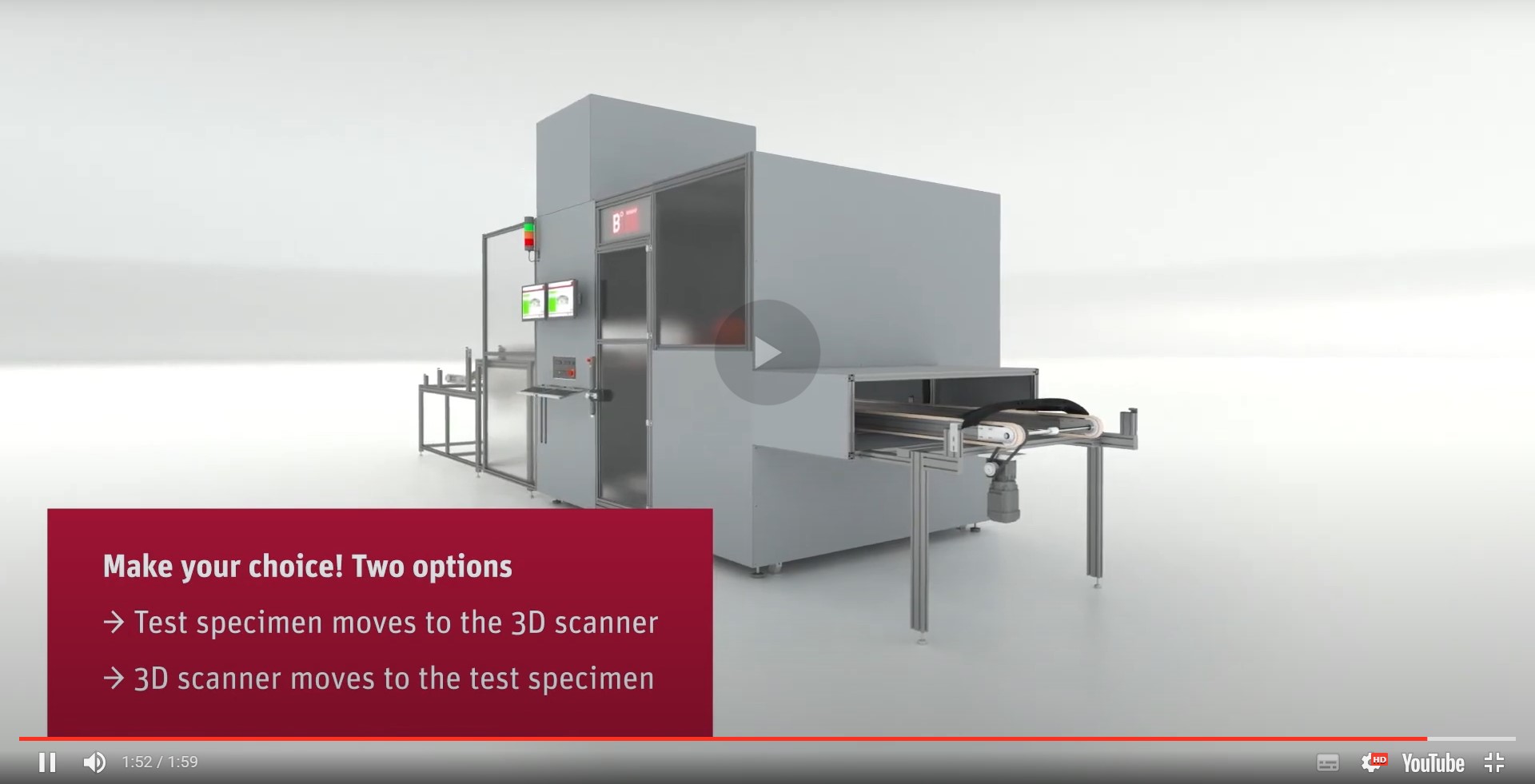
Videoclip Smart Component Tester
Function
- As an individual test bench or end-of-line-tester in the production line
- Testing the correct installation and position of components
- Short linear conveyor belt without workpiece carriers
- Exact determination of the component position and the respective model
- Quick and safe take-up of the test specimen
- Quick detection of components via 3D scanner
- Scan comparison with a master stored in the system
- Independence of contrast and light conditions
- Results can be flawlessly reproduced
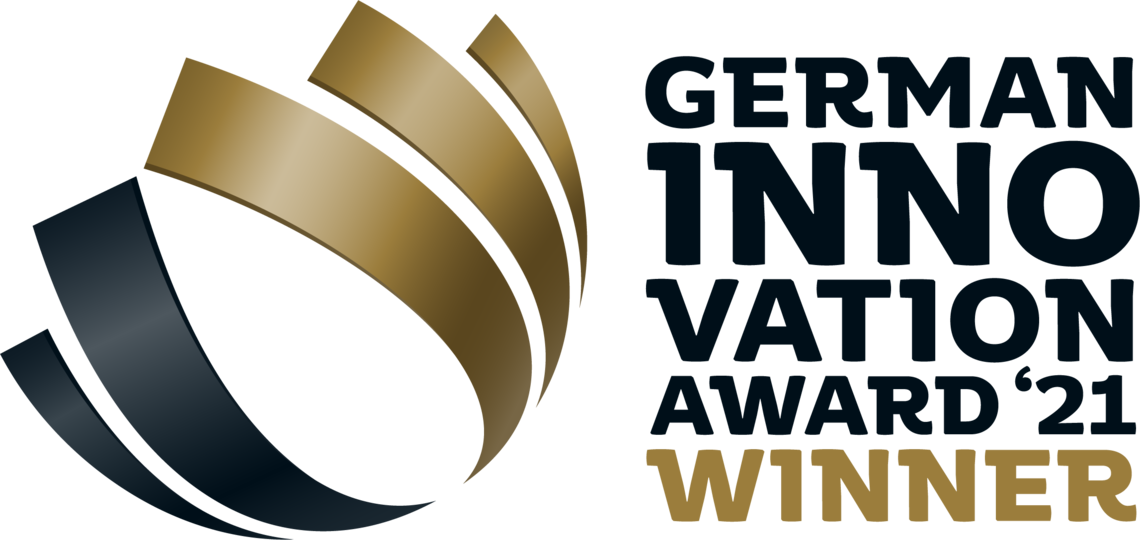
Advantages
- New concept: version-independent and flexible EOL testing
- Flexible: handling of differently painted surfaces and different components
- Simple and compact: no workpiece carriers – mechanical setup saves production space, retrofitting effort, testing time and costs
- Mixed operation of all versions implemented in the test system
- High level of flexibility for future testing tasks: quick and easy adding of new models using the user interface
- No set-up times: linear conveyor belt instead of individual workpiece carriers – test specimens lie freely on top
Radar test systems
Already for today’s driver assistance systems – but especially with regard to autonomous driving – fully functional radar systems in vehicles are essential for the safety of all road users. High-quality bumpers and radomes, behind which the radar sensors are located, therefore require above all one feature: a consistently well penetrability of the used material. Inhomogeneous materials, such as sparsely applied varnishes in places, can lead to distorted or attenuated signals, which ultimately poses a risk to pedestrians and cyclists. Therefore, in order to prove admissibility for autonomous driving, all relevant painted components in the vehicle are to check for their radar capability.
With a cycle time of less than 15 seconds for testing an area of around one square meter, these test systems from Berghof Automation are in the top group in this product segment. In the area of Berghof radar test systems, you can optionally choose between two variants in order to test the reflection and transmission of your components quick and reliable. Based on using our solutions you are sure to deliver a consistently high quality of products to your customers.
Variant 1: Testing the radar attenuation of the radiator grill
- Cabin with cross table (available measuring range up to 500 x 400 mm)
- Quick-change system similar to the standardized coupling of our latest bumper test system
- Automatic moving procedure of the test sample
- Your advantage: Very precise testing, because there is no overall conical test. The Berghof solution measures individual points, which is a much more precise testing procedure.
Variant 2: Fully automated testing of the radar attenuation of bumpers
- Test cabin for the mountings of driverless transport systems (DTS)
- Mixed operation available (possibility to test different variants with one Berghof system)
- Mounting of the measuring clamp on the robot arm
- High flexibility, which is to use for other variants or later models too
How can we help you?
We look forward to receiving your call or e-mail. You are also welcome to send us a message using our contact form. We will be there for you as soon as possible.