A high degree of automation increasingly requires the flexible integration of individual safety functions, which makes a programmable safety controller truly state-of-the-art when it comes to future-oriented, competitive machines and systems. The innovative and integrated safety solution from Berghof includes a freely programmable CODESYS safety PLC and a safety I/O module according to the requirements of safety standards such as IEC 61508 SIL 3 and DIN EN ISO 13849-1 PLe.
Integrated and CODESYS Programmable Safety Solution
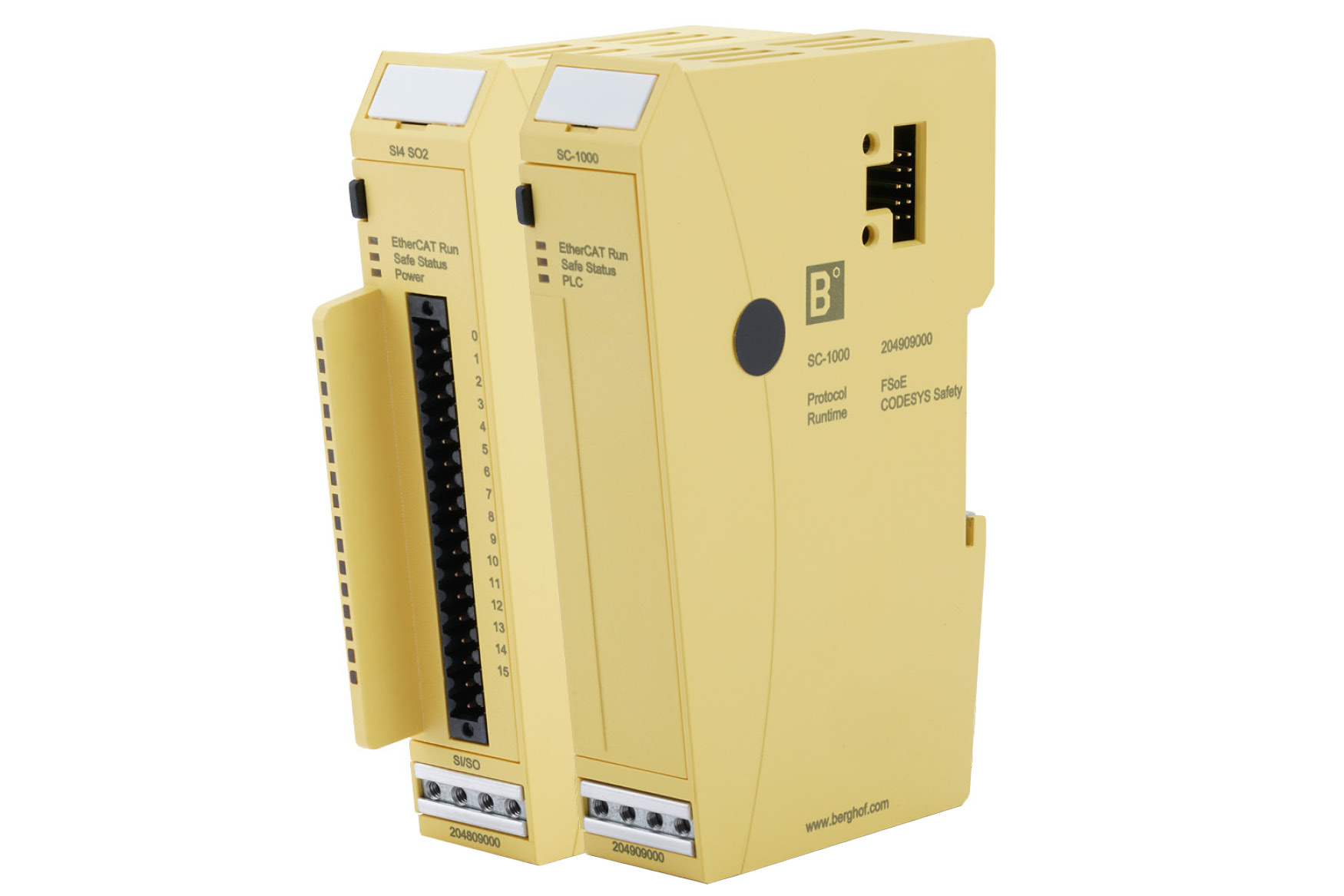
Saving costs with safety
Modern safety concepts are mandatory today. Together with programmable safety technology, they offer a competitive advantage for machine and system manufacturers. The comprehensive process overview ensures better error localization and diagnostics in the event of an error. This minimizes system downtimes.
A safe application
The development environment provided by Berghof allows users to design the safety-related and functional parts of the application in an integrated manner. Despite the great degree of freedom this entails, the stringent demands on safety applications are met without exception.
In order to enable project planners to accomplish their tasks in the best possible way, Berghof complies with the challenging PLCopen safety standard. The specifications defined for PLCopen safety are implemented consistently in two levels of programming rules. The basic level provides the user with certified function blocks, while the extended level offers nearly limitless possibilities in terms of safety-related functions.
Berghof does not limit the scope of functions and additionally offers further verification mechanisms for safe programming. The additional functions for securing all created safety applications are regarded as a matter of course. The number of usable modules is only limited by the memory of the device.
This spectrum of services offers nearly limitless possibilities to the user. Common safety devices for operating elements, sensors or output signal monitoring pose just as little of a challenge as sophisticated safety functions, entirely according to the requirements of the specific task.

CODESYS is considered one of the best and most popular manufacturer-independent programming standards. Berghof offers this standard in its most comprehensive, unmodified form and, in this way, provides numerous advantages to customers and end users alike.
Most common safety concepts tend to focus on the hardware, but forget the needs of the user with regard to enabling reasonable software integration.
Berghof’s safety package optimizes the interaction between hardware and software For the user, there are no boundaries between “safety” and “non-safety” components, which significantly streamlines the programming and configuration work. As a result, you can exchange diagnostics, status and signal-switching information effortlessly between the two levels.
Thanks to its full integration in the CODESYS standard, this solution offers clear added value compared to other safety solutions on the market.
Safety must be addressed in an expert manner
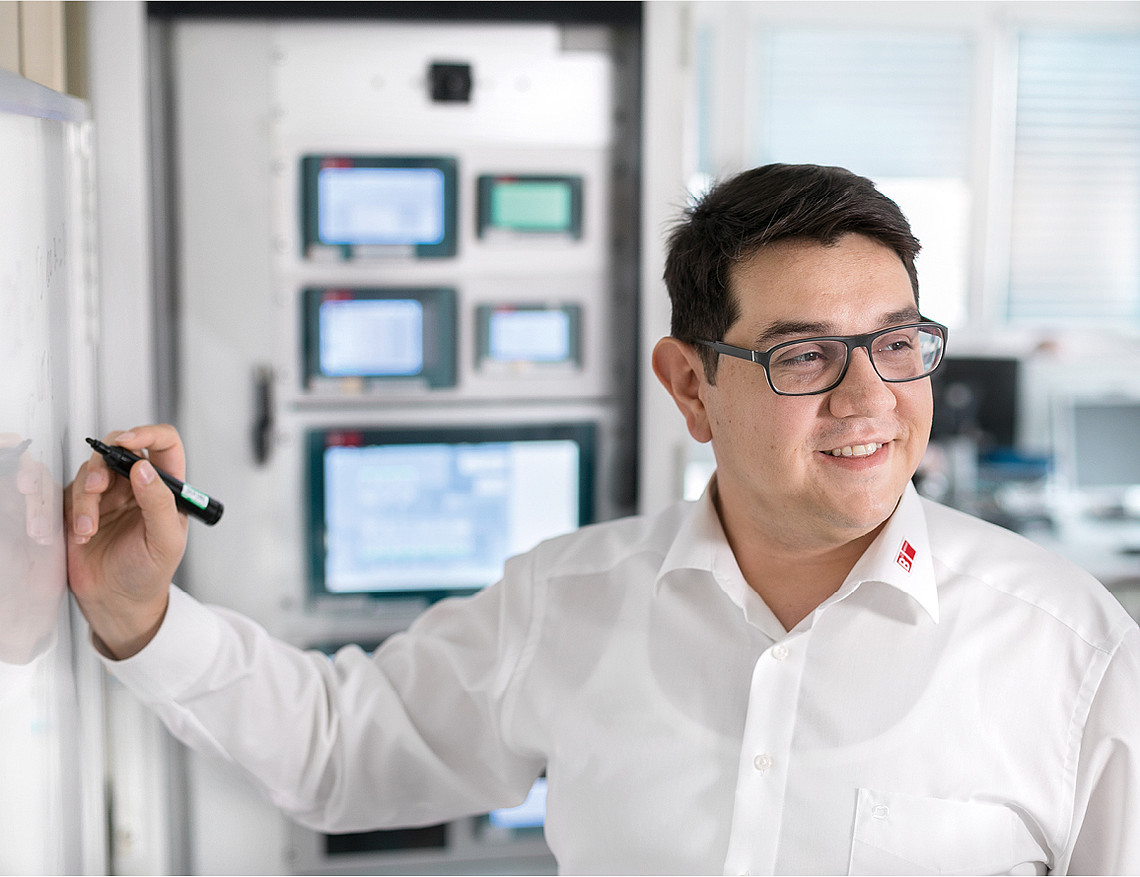
Berghof does not leave this important aspect to chance and provides training to its users in all safety-relevant topics to ensure the safe operation of both hardware and software.
The fundamentals are taught in the corresponding training modules:
- Working with the CODESYS Safety Plug-In
- Working with CODESYS versions in compliance with safety requirements
- Integration of safety components into a project
- Safety-related target system settings
- Creating a safety application
- Presentation of the most common safety modules
- Special use of the safety components
- Bringing controllers to a safe state
- Data exchange between the safety CPU and the main CPU
- Application examples
- Q&A based on your individual needs
How can we help you?
We look forward to receiving your call or e-mail. You are also welcome to send us a message using our contact form. We will contact you as soon as possible.